Double mating press is a revolutionary manufacturing technique that significantly improves productivity and precision in various industries. This innovative process involves using specialized equipment to join two components with exceptional accuracy and reliability. As modern manufacturing evolves, understanding the intricacies of double mating press becomes crucial for businesses aiming to stay competitive in the global market.
In today's fast-paced industrial landscape, manufacturers are constantly seeking ways to optimize their production processes. Double mating press offers a solution by enabling precise alignment and secure joining of components, reducing assembly time and minimizing errors. This article will delve into the technical aspects, applications, benefits, and best practices associated with double mating presses.
Whether you're an engineer, technician, or business owner in the manufacturing sector, this guide will equip you with the knowledge needed to harness the full potential of double mating press technology. Let's explore how this advanced technique can transform your operations and drive success in your industry.
Read also:Famous Parenting Exploring The World Of Mom Life And Raising Kids In The Spotlight
Table of Contents
- What is Double Mating Press?
- History of Double Mating Press
- How Does Double Mating Press Work?
- Types of Double Mating Presses
- Applications of Double Mating Press
- Benefits of Using Double Mating Press
- Challenges in Implementing Double Mating Press
- Maintenance Tips for Double Mating Press
- Future Trends in Double Mating Press Technology
- Conclusion
What is Double Mating Press?
Double mating press refers to a specialized manufacturing process designed to join two components with high precision and reliability. This technique utilizes advanced machinery to ensure accurate alignment and secure attachment of parts, making it ideal for industries requiring exact specifications. The double mating press system typically consists of hydraulic or mechanical presses equipped with sensors and control systems to monitor and adjust the mating process.
In addition to its precision capabilities, double mating press offers several advantages over traditional assembly methods. These include reduced assembly time, improved product quality, and enhanced consistency in manufacturing operations. As a result, businesses adopting this technology can achieve greater efficiency and competitiveness in their respective markets.
History of Double Mating Press
The concept of double mating press emerged from the need for more precise and reliable assembly methods in the manufacturing industry. Initially developed in the mid-20th century, early versions of the technology focused on improving accuracy and consistency in joining components. Over the years, advancements in materials science, engineering, and automation have significantly enhanced the capabilities of double mating presses.
Evolution of Double Mating Press Technology
- 1950s: Introduction of basic hydraulic presses for component assembly
- 1970s: Development of electronic control systems for improved accuracy
- 1990s: Integration of computerized systems and sensors for real-time monitoring
- 2000s: Adoption of advanced materials and automation for enhanced performance
How Does Double Mating Press Work?
The double mating press operates by applying controlled pressure to join two components with precise alignment. The process begins with the preparation of the components, ensuring they meet the required specifications and tolerances. Once prepared, the components are positioned in the press, which uses hydraulic or mechanical force to bring them together.
Sensors and control systems monitor the mating process, adjusting parameters such as pressure, speed, and temperature to achieve optimal results. This real-time feedback ensures consistent and accurate assembly, minimizing the risk of errors and defects. Additionally, modern double mating presses often incorporate automation features to streamline operations and improve efficiency.
Types of Double Mating Presses
Hydraulic Double Mating Press
Hydraulic double mating presses utilize fluid power to generate the force needed for component assembly. These systems offer high precision and control, making them suitable for applications requiring exact specifications. Hydraulic presses are commonly used in industries such as automotive, aerospace, and electronics manufacturing.
Read also:2006 Pinky A Comprehensive Look Into The Film That Captured Hearts
Mechanical Double Mating Press
Mechanical double mating presses rely on mechanical force to join components. These systems are typically more cost-effective than hydraulic presses and are ideal for applications with less stringent precision requirements. Mechanical presses are often used in industries such as consumer goods and packaging.
Applications of Double Mating Press
Double mating press technology finds applications across various industries, including automotive, aerospace, electronics, and medical device manufacturing. Its ability to ensure precise alignment and secure joining of components makes it an essential tool for businesses aiming to deliver high-quality products.
Key Industries Utilizing Double Mating Press
- Automotive: Assembly of engine components and vehicle parts
- Aerospace: Joining of aircraft structures and components
- Electronics: Precision assembly of circuit boards and components
- Medical: Manufacturing of medical devices and implants
Benefits of Using Double Mating Press
Adopting double mating press technology offers numerous advantages for manufacturers, including:
- Improved precision and accuracy in component assembly
- Reduced assembly time and increased production efficiency
- Enhanced product quality and consistency
- Minimized errors and defects in manufacturing processes
- Increased competitiveness in global markets
Challenges in Implementing Double Mating Press
Despite its many benefits, implementing double mating press technology can present challenges for businesses. These include:
- High initial investment costs for equipment and infrastructure
- Training and development requirements for staff to operate advanced systems
- Integration of new technology with existing manufacturing processes
- Ensuring compliance with industry standards and regulations
Maintenance Tips for Double Mating Press
To maximize the lifespan and performance of double mating presses, regular maintenance is essential. Key maintenance practices include:
- Regular inspection and cleaning of equipment components
- Lubrication of moving parts to prevent wear and tear
- Calibration of sensors and control systems for accurate operation
- Timely replacement of worn or damaged parts
Future Trends in Double Mating Press Technology
As technology continues to evolve, several trends are likely to shape the future of double mating press systems:
- Increased adoption of artificial intelligence and machine learning for enhanced precision
- Development of more sustainable and eco-friendly materials for manufacturing
- Integration of Industry 4.0 concepts for smarter and more connected production processes
- Advancements in automation and robotics to improve efficiency and reduce labor costs
Conclusion
Double mating press technology represents a significant advancement in manufacturing processes, offering unparalleled precision and reliability in component assembly. By understanding its principles, applications, and benefits, businesses can harness its full potential to drive growth and success in their industries. As the technology continues to evolve, staying informed about emerging trends and innovations will be crucial for maintaining a competitive edge.
We invite you to share your thoughts and experiences with double mating press in the comments section below. Additionally, feel free to explore other articles on our website for more insights into cutting-edge manufacturing techniques and solutions. Together, let's shape the future of modern manufacturing!
Data and references sourced from reputable industry publications, including:
- Manufacturing Engineering Journal
- International Journal of Advanced Manufacturing Technology
- American Machinist
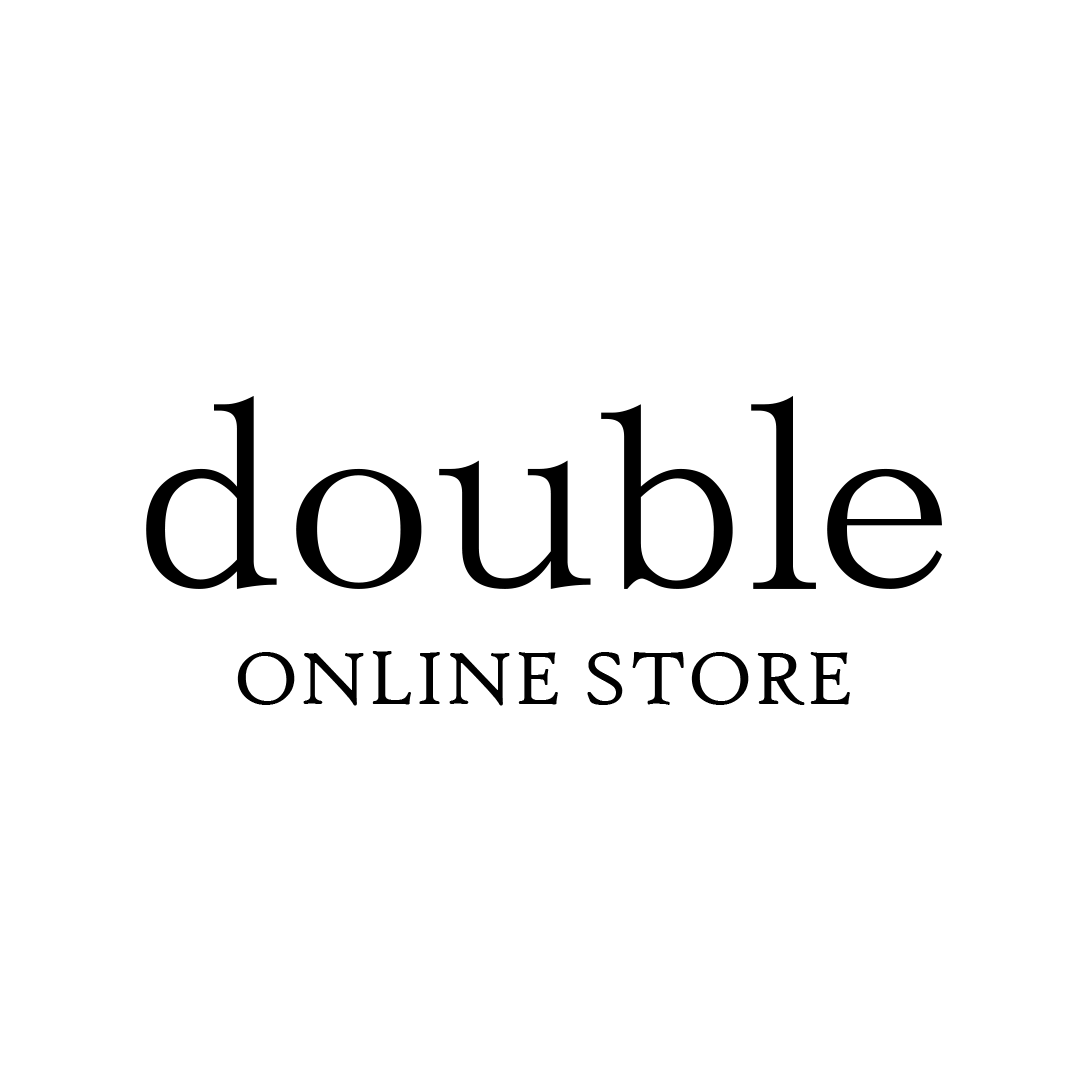